派瑞林用于航空设备的讨论
“ 星球大战:第四集 - 新希望”中的高潮结束 战 是电影史上最令人兴奋和激动人心的场景之一。Luke Skywalker和theRebels对帝国舰队进行了绝望的攻击。未能摧毁Empire可怕的死星将对该星系造成毁灭性后果。驾驶他的TIE战斗机,邪恶的Darth Vader正在调查LukeSkywalker的X翼并将其锁定在目标上。就在看来allhope失败的时候,救赎的Han Solo和他忠诚的Wookie同伴Chewbacca意外地在千禧猎鹰的最后一刻到达,以便从Vader中大大地阻止卢克。卢克信任部队,在战斗站的热排气口发射质子鱼雷,导致爆炸性的连锁反应和死星的毁灭。
tubeembed
受到多翼X翼星际战斗机的鼓舞,并且由于他们相信任务的重要性,反叛联盟通过实现击败邪恶帝国的目标找到了新的希望。与反叛联盟一样,航空航天也需要飞行员操作,以便安全地完成任务。先进的电子设备和有价值的组件用于飞行管理,现代飞机和战斗机,用于飞行管理,控制,仪表,导航,通信,传感器和发电,必须可靠地执行。这些先进的电子材料需要卓越的性能,其中重量,可靠性,信号完整性,衰减和承受强烈环境的能力对电路设计至关重要。随着航空航天工业性能要求的不断提高,
航空航天的首选保护
涂层多年来,喷涂,浸涂和刷涂的液态保形涂料为航空航天电子产品提供了一定程度的保护。但是,它们根本无法提供先进创新技术所需的保护级别。例如,传统涂层有可能在涂层中或下面捕获气泡。如果这些气泡在高海拔环境中或在太空操作期间打开,则可能导致暴露的电路发生故障。 Parylene 经过真空沉积过程,因此不存在捕获气泡的可能性。Parylene是一种透明的薄膜保形涂料,可以在涂有它的电子设备上增加一层。
Parylene保形涂料 在当今的电子产品中发挥着至关重要的作用,它具有出色的缝隙和多层渗透性,无与伦比的阻隔性能,低渗透性气体和湿气,抗紫外线性和极高的热稳定性。航空航天电子设备也经常承受连续振动和极端温度,尤其是地球的绝缘环境。这些苛刻的情况会损害无保护的电子设备,导致数据丢失,无法接收飞行期间所需的重要信息。通过makingsure采取了适当的预防措施,可以大大减轻飞机从危险电流和故障状况的损害。聚对二甲苯能够承受航空航天应用中遇到的极端温度和压力条件。
航空航天ParyleneCoating
Parylene涂层已经在整个航空航天工业中用于电子电路的所有领域,包括在空间的极端条件下暴露于湿气,冷凝,化学侵蚀,溶剂,零下温度或紫外线的那些。Parylene保形涂层符合要求,并显着延长了有价值的部件的安全寿命,例如工业级传感器,飞机照明中的LED,布线和布线组件,COTS,辐射探测器等等。
如果存在导致系统失效的时间错误功能,则极高的价值和人的生命可能会丢失。因此,重要的是尽一切努力以最好地保护关键部件。用于航空航天应用的PCA(印刷电路组件)必须保持严格的规范并承受恶劣的环境条件。这些组件经过一系列测试,包括高/低温,大气和温度冲击,耐化学性和防潮性,湿度和可燃性。
结论
为了避免破坏性后果,Parylene涂层越来越多地被用于提高创新和复杂技术的可靠性.Parylene已经成为复杂的航空应用的首选保护涂层,因为它能够在特定条件下,在特定时期内提供可靠的保护。时间,没有失败。
星球大战 俘获了许多世代的心灵和思想,因为它具有史诗般的故事情节,其惊人的特效以及引人入胜的音乐。此外,它带来了乐观,创造力,也许最重要的是希望。性相似 星球大战,聚对二甲苯涂层提供创造性地解决问题foraccelerated和不断发展的技术。如果你仍然不相信Paryleneis是优质的保形涂层,Darth Vader可能会说,“我发现你的缺乏令人不安的事情。”
Para-Coat技术公司通过 制定良好的商业战略并相信Parylene 涂层工艺的重要性而受到鼓舞, 并通过多年的服务保持了高水平的信任,以满足所有要求的性能标准。通过设定Parylene沉积效率的标准,我们提供客户启发的解决方案,并 希望您将利用我们的专业知识。
The climactic end battlein Star Wars: Episode IV – A New Hope is one of the mostsuspenseful and thrilling scenes in cinema history. Luke Skywalker and theRebels launch a desperate attack on the Imperial fleet. Failure to destroy theEmpire’s dreaded Death Star will have devastating consequences to the galaxy.Piloting his TIE fighter, the evil Darth Vader is zeroing in on LukeSkywalker’s X-wing and has it locked in on target. Just when it seems that allhope is lost, the redeeming Han Solo and his loyal Wookie companion, Chewbacca,unexpectedly arrive at the last moment in the Millennium Falcon to dramaticallysave Luke from Vader. Luke with trust in the Force, fires proton torpedoes atthe thermal exhaust port of the battle station leading to an explosive chainreaction and the destruction of the Death Star.
tubeembed
Encouraged by theversatile X-wing Starfighter and because of their belief in the importance ofthe mission, the Rebel Alliance found renewed hope by accomplishing their goalin defeating the evil Empire. Like the Rebel Alliance, aerospace also hasaircraft operating that require more than a pilot in order to safely completeeach mission. Advanced electronics and valuable components are used inspacecraft, modern aircraft, and fighter jets for flight management, control,instrumentation, navigation, communication, sensors, and power generation thatmust perform reliably. These advanced electronic materials require superiorperformance where weight, reliability, signal integrity, attenuation, andability to withstand intense environments are critical to the circuit design.As demands for performance in the aerospace industry continue to increase, it’scrucial to provide adequate protection to enhance the reliability of theircomplex technologies.
The Protective Coatingof Choice for Aerospace
For a number of years, liquid conformal coatings that are sprayed, dipped, andbrush applied offered a level of protection for aerospace electronics. However,they simply do not offer the level of protection that is required in advancedinnovative technologies. For instance, traditional coatings have the potentialto trap air bubbles in or underneath the coating. If these air bubbles were toopen in an environment at high altitudes or during space operations, it canpotentially cause the exposed circuit to fail. Parylene goes through avacuum deposition process, so there is no potential for the trapping of airbubbles. Parylene is a transparent, thin film conformal coating that adds noweight to the electronic device on which it is coated.
Parylene conformal coatings playa critical role in today’s electronics by offering excellent crevice andmulti-layer penetration, unrivaled barrier properties with low permeability togases and moisture, and UV resistance and extreme high thermal stability.Aerospace electronics are also routinely subjected to continuous vibration andextreme temperatures especially above the insulating atmosphere of the earth.These demanding situations can impair unprotected electronics and cause a lossof data and failure to receive vital information necessary during flight. By makingsure the proper precautions have been taken, damage to an aircraft fromhazardous currents and faulty conditions can be greatly mitigated. Parylene isable to withstand the extreme temperature and pressure conditions encounteredin aerospace applications.
Aerospace ParyleneCoating
Parylene coatings have been used throughout the aerospace industry in all areasof electronic circuitry including those exposed to moisture, condensation,chemical attack, solvents, sub-zero temperatures, or UV-rays in the extremeconditions of space. Parylene conformal coating meets the requirements andprolongs the safety lifetime significantly for valuable components such as,industrial grade sensors, LEDs in aircraft lighting, wiring and cablingassemblies, COTS, radiation detectors, and much more.
Extremely high valuesand human lives are at the risk of being lost if there are ill-timedmalfunctions causing systems to fail. Therefore, it is important to make everyeffort for the best possible protection of the vital components. PCAs (PrintedCircuit Assembly) for aerospace applications must maintain strictspecifications and withstand aggressive environmental conditions. Theseassembles undergo a series of tests including high/low temperature, atmosphericand temperature shock, chemical and moisture resistance, humidity, andflammability.
Conclusion
In order to avoid devastating consequences, Parylene coatings are increasinglybeing used to enhance the reliability of innovative and complex technologies.Parylene has become the protective coating of choice for sophisticatedaerospace applications because of its ability to provide reliable protectionunder specific conditions, for a specified period of time, without failure.
Star Wars capturedthe hearts and minds of many generations because of its epic storytelling, itsvisually stunning special effects, and its spellbinding music. In addition, itinspired optimism, creativity, and perhaps most importantly, hope. Similarto Star Wars, Parylene coating offers creative problem solving foraccelerated and evolving technology. If you still don’t believe that Paryleneis the superior conformal coating, Darth Vader might say, “I find your lack offaith disturbing.”
Encouraged by having agood business strategy and a belief in the importance of the Parylene coatingprocess, Para-Coat Technologies establishedand has maintained a high level of trust with years of service through acommitment to meet every required performance standard. By setting the standardfor Parylene deposition efficiency, we offer customer-inspired solutionsand hopeyou will take advantage of our expertise.
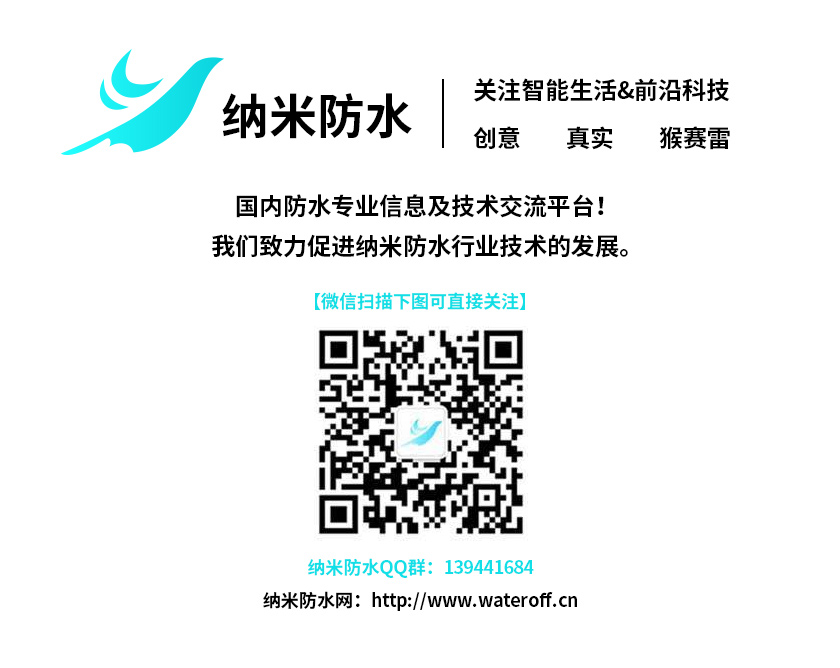
随着电子产品防水需求的不断提高,从原先的 IP54到现在的IP67IP68等级!市场上出现了防水透气膜和防水透音膜,目前这两种不同的材料应用被搞混了,今天便与大家一起讨论防水透气
最近各地降雨量激增,所以手机就难免会沾点水,作为生活中不可或缺的电子产品,防水已经成为一个十分重要重要功能,而且个人对目前的IP68手机市场是相当不满意的。为什么?太贵
自然界中荷叶具有出淤泥而不染的典型不沾水特性(学术上称为Cassie-Baxter状态),具有自清洁、抗结冰、减阻、抗腐蚀等广泛应用价值,而玫瑰花瓣则具有水滴高粘附特性(称为Wenze
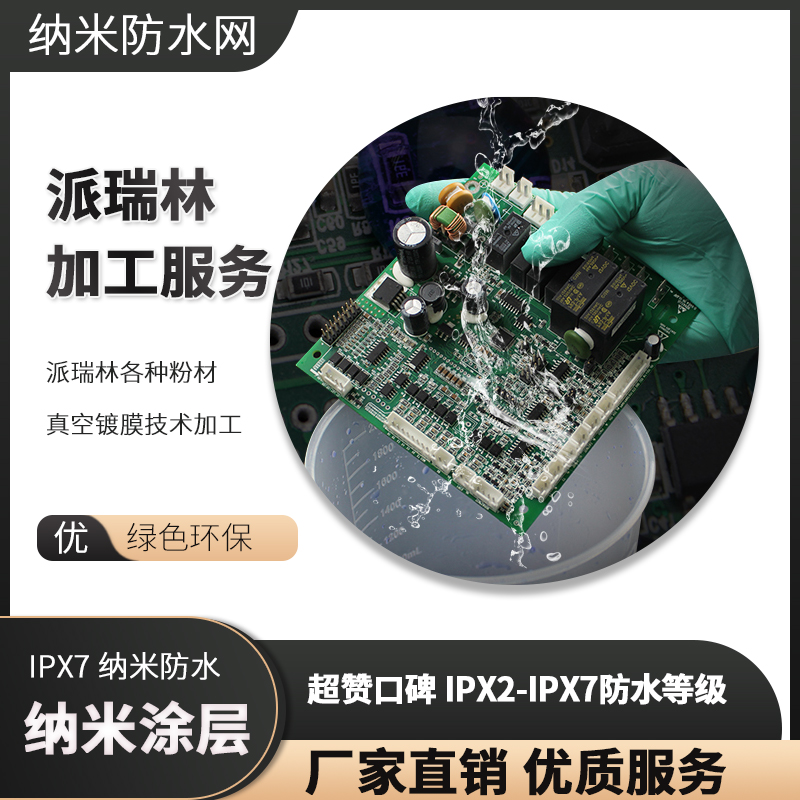
派瑞林各种粉材真空镀膜技术加工 纳米涂层防水处理
派瑞林各种粉材真空镀膜技术加工 纳米涂层防水处理
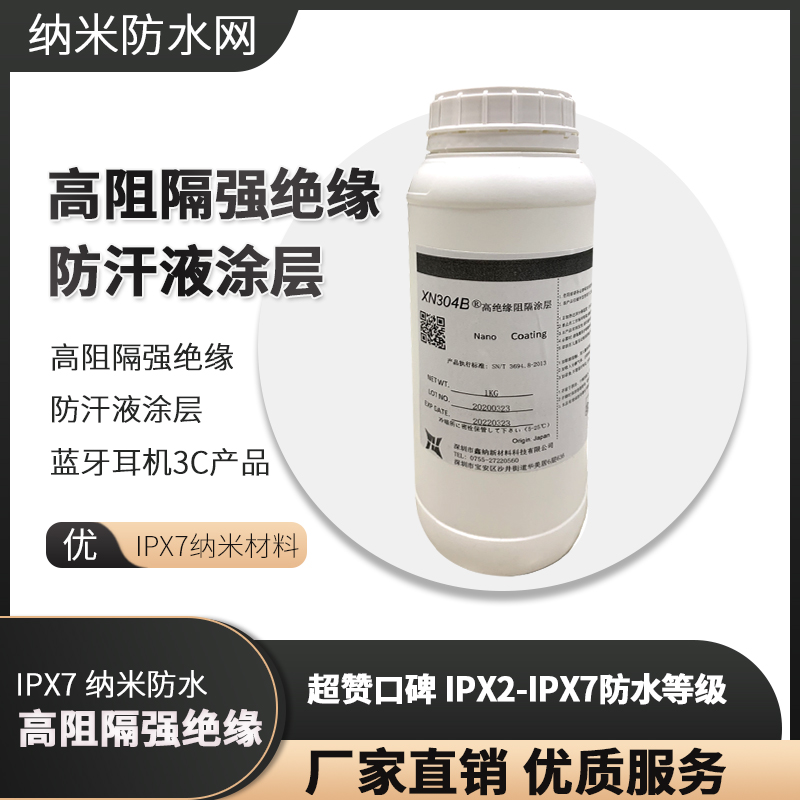
高阻隔强绝缘防汗液涂层蓝牙耳机3C电子产品IPX7纳米材料
高阻隔强绝缘防汗液涂层蓝牙耳机3C电子产品IPX7纳米材料
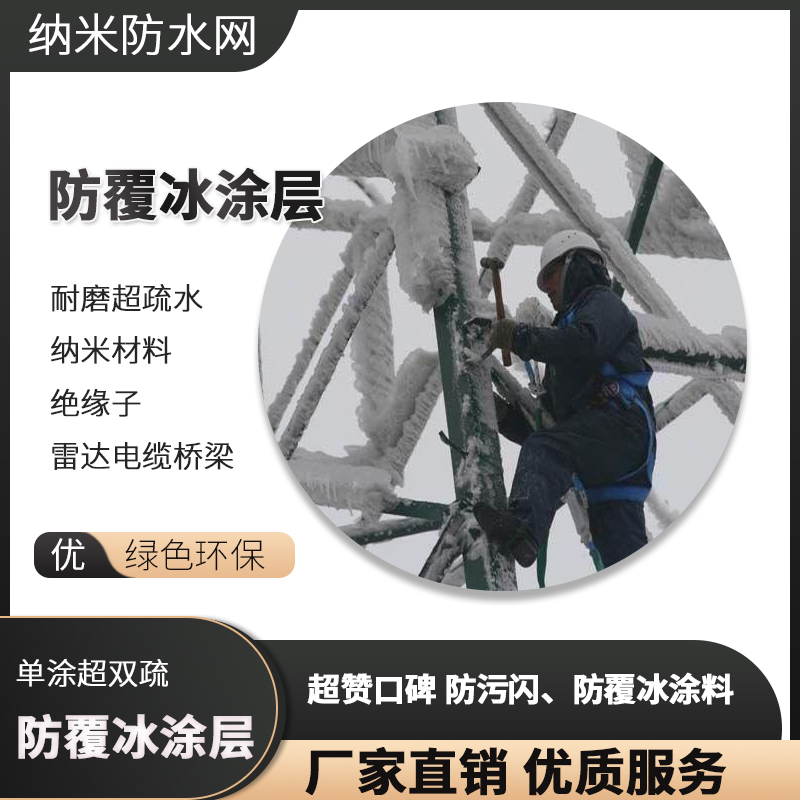
耐磨超疏水纳米材料 绝缘子架空导线电缆桥梁防覆冰涂层
耐磨超疏水纳米材料 绝缘子架空导线电缆桥梁防覆冰涂层
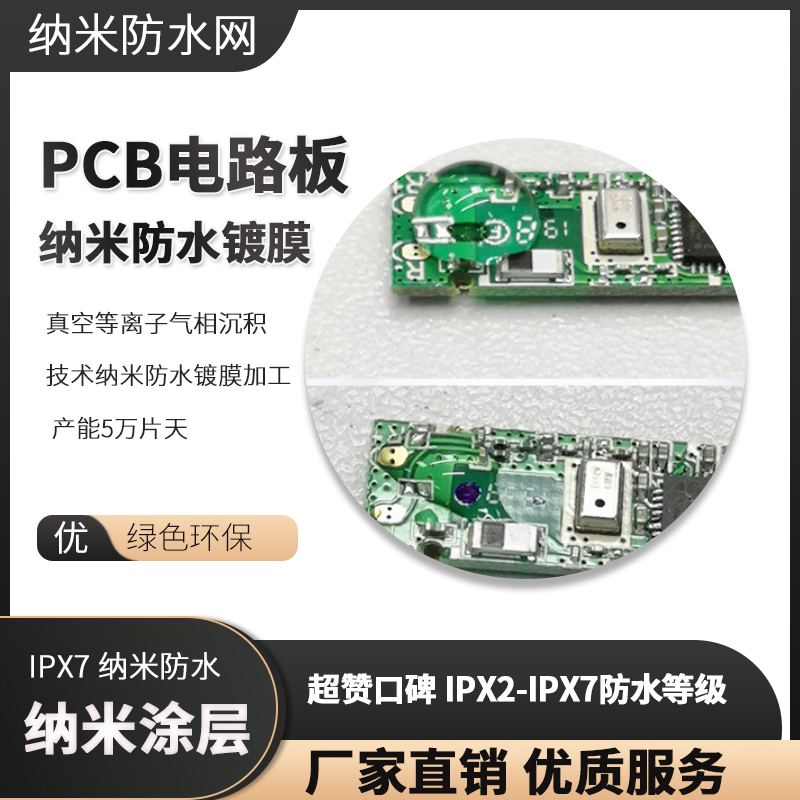
真空等离子气相沉积技术纳米防水镀膜加工 产能5万片天
真空等离子气相沉积技术纳米防水镀膜加工 产能5万片天
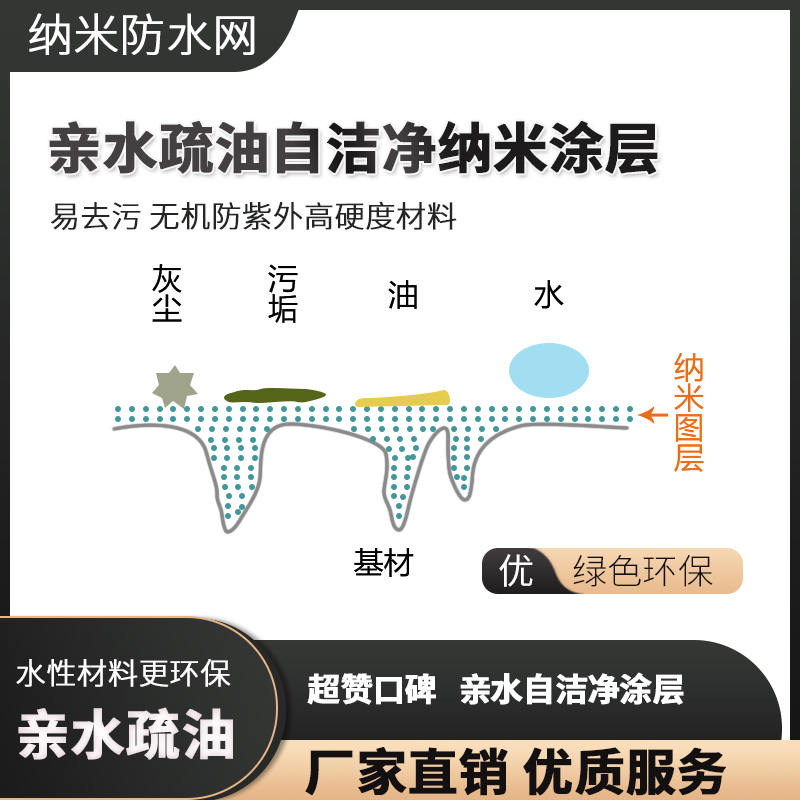
亲水疏油自洁净纳米涂层 易去污 无机防紫外高硬度材料
亲水疏油自洁净纳米涂层 易去污 无机防紫外高硬度材料

台湾超亲水防雾塑料专用 附着力好 透过率高 持久有效
台湾超亲水防雾塑料专用 附着力好 透过率高 持久有效