[派瑞林日记]我可以加紫外荧光剂到派瑞林涂层吗?
三防漆和紫外荧光剂
三防漆通过各种操作环境为印刷电路板(PCB)和类似电气组件提供出色的保护,保护其化学,电气和/或机械性能。
涂层的可靠性根据涂层材料和使用条件而变化。如果要将PCB直接暴露在紫外线下,大多数三防漆都需要专门的加工和检验程序。肉眼看不见,紫外线辐射的波长在100-400纳米(nm)之间。向涂层中添加UV通常荧光剂用于液体保形涂料中以用于检查目的,但是对于聚对二甲苯使用具有显著的缺点。
Parylene一再表现出卓越的实用性,超越了大多数竞争性涂料(包括丙烯酸,环氧树脂,硅树脂和聚氨酯)作为生物,消费品,工业,医疗和军事系统基材的性能,包括:纳米防水网:http://www.wateroff.cn/
·对部件形状的适应性,
·介电强度,
·耐用,灵活的部件保护,
·绝缘性能,
·无针孔均匀涂层,
·耐化学品和溶剂。
此外,与竞争对手相比,聚对二甲苯涂层可以以超薄层施加,在最终产品上通常不会检测到厚度水平的显着保护。
聚对二甲苯和紫外线
尽管其作为保形涂层具有许多应用和特性,但大多数聚对二甲苯品种对UV辐射的总体耐受性是有限的。虽然在室内保持稳定,但大多数聚对二甲苯配方不建议在直射阳光下长期操作环境下使用。
也就是说,聚对二甲苯C和N的UV稳定性很少超过100小时; 聚对二甲苯AF-4在这方面是优越的,当按照现行的ASTM G 154标准进行测试时,提供2,000小时或更长时间的紫外线防护。这种性能水平还超过了由丙烯酸,环氧树脂,硅树脂和聚氨酯制成的竞争性保形涂层。
紫外荧光剂和聚对二甲苯
在大多数液体保形涂层处理的检查阶段使用UV荧光剂。但是,在聚对二甲苯涂层的情况下,必须注意以下原因:
·UV微量添加剂不是聚对二甲苯二聚体的一部分,必须在涂覆前加入。
·紫外荧光材料的分子结构大于聚对二甲苯分子。
·Parylene材料保留了渗透掩蔽的能力,三十UV荧光剂不能渗透。
·因此,粗略检查可能无法检测无涂层区域内的UV材料。
·该组件可以通过检查,授权和清除其设计的功能,即使这些缺陷未被检测到。
常包括均匀的荧光剂,但是聚对二甲苯不具有。在UV光检测期间,UR,AR和SR涂层发出明亮而清晰的荧光。它们清楚地表明了痕迹在涂层中的精确位置,在涂层中已经存在并且尚未应用。
在这些情况下,假定向聚对二甲苯二聚体中添加UV荧光正确地指示涂层是否渗透到任何无涂层区域是错误的。
·在沉积过程中,UV荧光剂往往会随机溅到PCB或其他组件上。
·在某些情况下,UV荧光剂的不均匀支付可能导致材料随意划伤。
·无论是否采取措施减轻这些可能性,其他PCB都可能完全没有紫外荧光剂。
通过基于这些不可靠结果的检查来通过组件不仅会导致组件故障,而且还会导致潜在的危险结果,其中通过坚固耐用或类似的专业操作条件来依赖组件以获得可靠的性能。
紫外固化和聚对二甲苯
用于保护保形涂料,粘合剂和油墨的光化学工艺,与常规固化技术相比,UV固化产生各种增值性能。将高强度紫外线照射到干燥(固化)涂层或其他物质上,紫外线固化可以提供即时效果,提高生产速度,同时减少对典型设置和清理过程的需求和数量。降低的操作成本和增加的生产能力是许多涂料和工艺的UV固化的进一步优点。
在这些情况下,涂层和基材之间的优异粘合是环保的,节省能源而无需排放控制。过程/产品拒绝的发生率降低提供了以下额外的好处:
·更好的附着力和粘合强度,
·耐用而有弹性的涂层表面,
·增强耐磨性/表面划伤性,
·具有更好的防止接触化学品和溶剂的保护。
在程序上,UV固化过程中必不可少的光化学反应将液体单体和低聚物与微量痕量的光引发剂混合,光引发剂随后暴露于UV能量。在紫外线固化过程中,紫外线与特殊配方的化学物质相互作用,比传统方法更快地固化涂层。光引发剂吸收来自处理光源的紫外线能量,无论是弧光还是激光。所得到的化学反应在几秒钟内将液体涂料配方转化为稳定的固化膜。
在沉积聚对二甲苯之后,如果存在任何掩蔽区域,则去除掩蔽材料。去掩蔽区域周围的聚对二甲苯薄膜通过去掩蔽过程最小程度地损坏是相当普遍的。这可能导致聚对二甲苯的“手指”或甚至大的撕裂。有时,创建的边缘必须密封,以防止任何湿气或其他化学物质渗入侧边的可能性。
可以通过施加液体保形涂层来修复这些边缘或其他缺陷。我们经常使用聚氨酯保形涂料,因为它最接近地显示聚对二甲苯的性质。有时我们的客户会要求我们使用UV固化液体修饰材料。但是,由于上述原因,我们不建议使用任何与聚对二甲苯涂层配合使用的UV固化机制,因为它会严重降低薄膜的性能。
尽管有效用于其目的,但这种方法与聚对二甲苯的化学气相沉积(CVD)工艺很大程度上不相容,严重限制了其与聚对二甲苯的适用性。
总 结
不推荐使用UV荧光剂和UV固化材料作为LED器具的聚对二甲苯敷形涂料的组分。
最重要的是要了解UV荧光剂不是原始聚对二甲苯二聚体的一部分。由于这种现实,组合这两种材料改变了沉积的保形涂层的组成,污染了聚对二甲苯的纯度。随后的聚对二甲苯-UV荧光剂杂化物可以通过检查,但通常不会比其它情况下更耐UV光。同时,由于引入了UV荧光剂污染物,因此使用聚对二甲苯保形涂层的基本导电,绝缘和保护性能将会降低。
绝对没有数据支持这种混合薄膜的任何改进性能,并且由于污染物的引入,UV荧光剂很可能最终会严重降低聚对二甲苯的性能。尽管如此,目前的证据表明,尽管大多数聚对二甲苯类型(C,D,N)的容量有限,无法为暴露于紫外光源的LED提供可靠的长期保护,但已设计出可用于外部LED使用的聚对二甲苯涂层。与UV荧光剂一样,对于聚对二甲苯是优选的保形涂层材料的众多应用中的任何一种,UV可固化涂层是组合的不良选择; 因此,它不应该用于涂抹聚对二甲苯。
英文原文
Conformal Coatings and UV Trace
Conformal coatings provide exceptional protection for printed circuit boards (PCBs) and similar electrical assemblies, through a wide variety of operating circumstances, safeguarding their chemical, electrical, and/or mechanical properties.
The reliability of coatings varies according to the coating material and conditions of use. Most conformal coatings require specialized processing and inspection procedures if PCBs are to be used in direct exposure to UV light. Invisible to the naked eye, UV radiation’s wave length registers between of 100-400 nanometers (nm). The addition of UV trace to coatings is commonly used in liquid conformal coatings for inspection purposes, but has significant drawbacks for parylene use.
Unsuitably of UV Treatments for Parylene Conformal Coatings
Parylene has repeatedly demonstrated superior utility in comparison to most competitive coatings – including acrylic, epoxy, silicone and urethane -- surpassing their performance as a substrate covering for biological, consumer, industrial, medical and military systems, in terms of:
· adaptability to component shape,
· dielectric strength,
· durable, flexible component protection,
· insulating properties,
· pinhole-free uniform coating, and
· resistance to chemicals and solvents.
In addition, parylene coatings can be applied in ultra-thin layers, compared to competitors’, providing significant protection at thickness levels are generally undetected on the final product.
Parylene and UV Light
Despite its many applications and assets as a conformal coating, the overall resistance of most parylene varieties to UV radiation is limited. While it remains stable indoors, most formulations of parylene are not recommended for long term use outdoors where exposure to direct sunlight is a condition of the operating environment.
That is, the UV stability of parylenes C and N seldom exceeds 100 hours; parylene AF-4 is superior in this respect, providing UV-protection for 2,000 hours or more, when tested according to the prevailing ASTM G 154 standards. This level of performance also exceeds competing conformal coatings produced by acrylic, epoxy, silicone and urethane.
UV Trace and Parylene
UV trace is used during the inspection stage of most liquid conformal coating processing. However, in the case of parylene coatings, care must be taken for the following reasons:
· The UV trace additive is not part of the parylene dimer and must be added prior to coating.
· The molecular structure of UV fluorescent materials is larger than that of parylene molecules.
· Parylene materials retain the ability to penetrate masking, even where those of UV fluorescents do not.
· Thus, cursory inspection may not detect UV material within the coating-free zone.
· The component may pass inspection, authorized and cleared for functions it is designed for, even as these flaws go undetected.
This is a problem for application of parylene coatings, in comparison to competitive conformal types, when a UV tracer is added. For instance, while urethane (UR), acrylic (AR) and silicone (SR) typically include a uniform fluorescing agent in their chemistry, parylene does not. During UV light inspection, UR, AR and SR coatings fluoresce brightly and clearly. They plainly indicate the precise location of the trace within the coating, where it has and has not been applied.
Under these circumstances, it is wrong to presume the addition of a UV florescent to the parylene dimer correctly indicates whether or not the coating has infiltrated any coating free zones.
· The UV trace tends to randomly splatter onto PCBs or other assemblies during its deposition process.
· Uneven disbursement of the UV trace can cause haphazard streaking of the material in some instances.
· Other PCBs may receive no UV trace at all, regardless of the care taken to alleviate these possibilities.
Passing the component through inspection based on these unreliable outcomes can not only lead to component malfunction, but also potentially dangerous outcomes, where the component is relied on for reliable performance through ruggedized, or similarly specialized, operating conditions.
UV Curing and Parylene
A photochemical process used to preserve conformal coatings, adhesives, and inks, UV curing generates a variety of value-added properties in comparison to conventional curing techniques. Applying high-intensity UV light to dry (cure) coatings or other substances, UV curing can provide instant results, increasing production speed while reducing the need for and number of typical set-up and clean-up processes. Lowered operating costs and increased production capacity are further advantages of UV curing for many coating materials and processes.
In these cases, the consequent superior bonding between coating and substrate is environmentally friendly, saving energy without need for emissions’ controls. The diminished incidence of process/product rejection offers the additional benefits of:
· better adhesion and bond strength,
· durable yet elastic coating surfaces, and
· enhanced resistance to abrasion/surface scratching,
· with improved protection against exposure to chemicals and solvents.
Procedurally, the photochemical reaction essential to the UV curing process mixes liquid monomers and oligomers with minute traces of photoinitiators, which are subsequently exposed to UV energy. In the UV curing process, ultraviolet light interacts with specially formulated chemistries to cure coatings more rapidly than possible with traditional methodologies. The photoinitiators absorb the UV energy from the process light source, either arc light or laser light. The resultant chemical reaction converts liquid coating formulation into a stable, cured film in a matter of seconds. 纳米防水网:http://www.wateroff.cn/
After parylene has been deposited, if there were any masking areas, the masking materials are removed. It is fairly common for the parylene film around the de-masking area to be minimally damaged by the de-masking process. This can result in “fingers” of parylene or even large tears. Sometimes, it is critical that the edges that were created be sealed to prevent any possibility of moisture or other chemicals penetrating the side edges.
These edges or other imperfections can be repaired via the application of a liquid conformal coating. We often use urethane conformal coating, as it most closely exhibits the properties of parylene. Sometimes our customers will request that we use a UV curable liquid touchup material. However, for the reasons outlined above, we do not recommend using any UV curing mechanism in concert with parylene coating, as it can severely degrade the film.
While efficient for its purposes, this approach is largely incompatible with parylene’s chemical vapor deposition (CVD) process, severely limiting its suitability for use with parylene.
Summary
Applying UV trace and touching up with UV cured material as components of parylene conformal coatings for LED appliances is not recommended.
Of paramount importance is understanding that the UV trace is not part of the original parylene dimer. Because of this reality, combining the two materials changes the composition of the deposited conformal coating, tainting the purity of the parylene. The consequent parylene-UV trace hybrid may pass inspection, but will typically not be any more resistant to UV light than it would otherwise have been. At the same time, the conductive, insulating and protective properties basic to the use of parylene conformal coatings will be diminished because of the introduction of UV trace contaminants.
Absolutely no data supports any improved properties of this hybrid film and, as a result of the introduction of the contaminant, it is highly likely that UV trace will ultimately degrade the parylene's performance, potentially in a serious way. Nevertheless, the current evidence shows that, despite the limited capacity of most parylene types – C, D, N – to provide dependable, longer-term protection for LEDs exposed to UV sources, parylene coatings have been devised that are useful for external LED use. As with UV trace, UV curable coating is a bad choice for combination for any of the numerous applications where parylene is the preferred conformal coating material; thus, it should not be used for touch up with parylene.
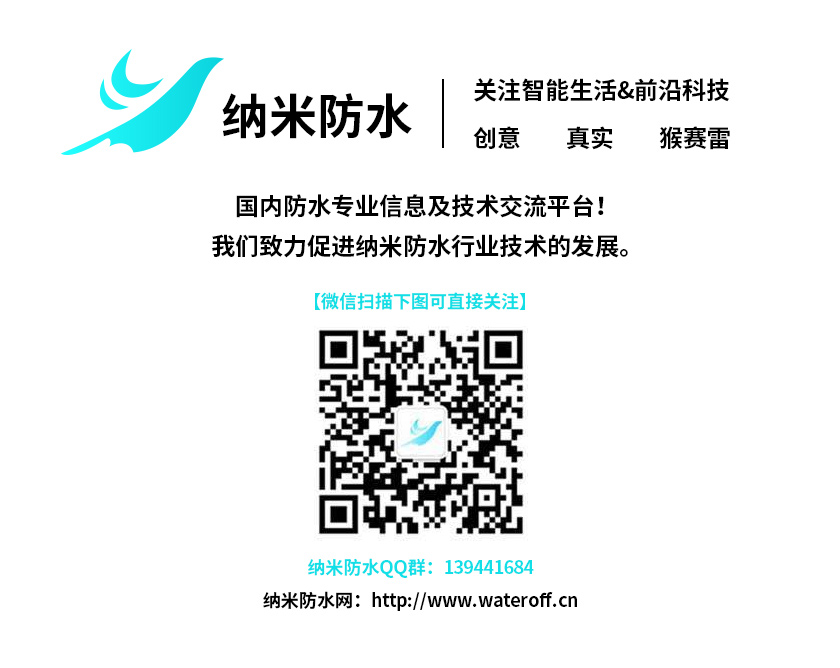
随着电子产品防水需求的不断提高,从原先的 IP54到现在的IP67IP68等级!市场上出现了防水透气膜和防水透音膜,目前这两种不同的材料应用被搞混了,今天便与大家一起讨论防水透气
最近各地降雨量激增,所以手机就难免会沾点水,作为生活中不可或缺的电子产品,防水已经成为一个十分重要重要功能,而且个人对目前的IP68手机市场是相当不满意的。为什么?太贵
自然界中荷叶具有出淤泥而不染的典型不沾水特性(学术上称为Cassie-Baxter状态),具有自清洁、抗结冰、减阻、抗腐蚀等广泛应用价值,而玫瑰花瓣则具有水滴高粘附特性(称为Wenze
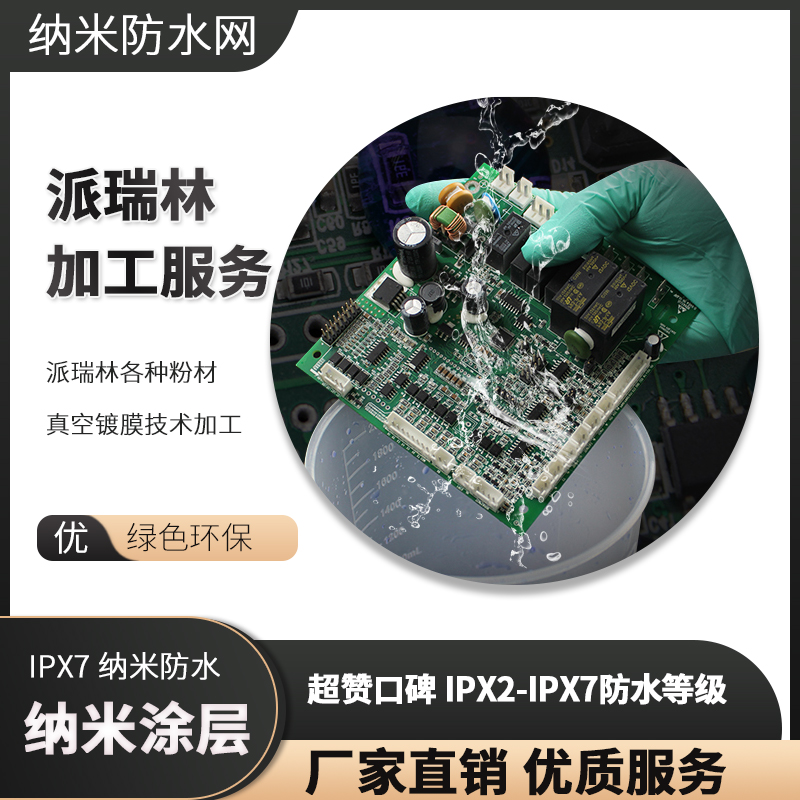
派瑞林各种粉材真空镀膜技术加工 纳米涂层防水处理
派瑞林各种粉材真空镀膜技术加工 纳米涂层防水处理
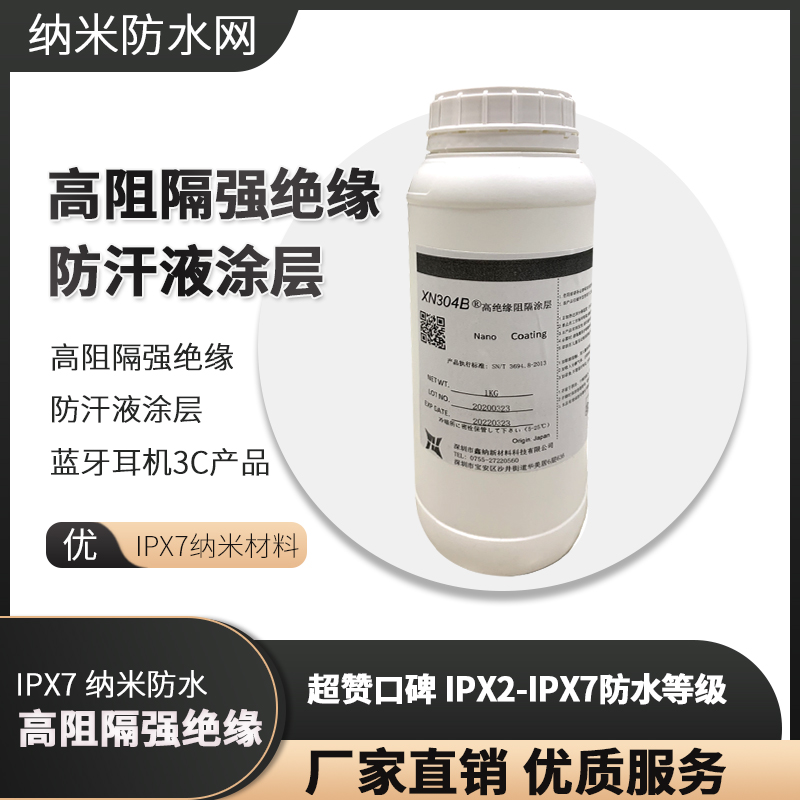
高阻隔强绝缘防汗液涂层蓝牙耳机3C电子产品IPX7纳米材料
高阻隔强绝缘防汗液涂层蓝牙耳机3C电子产品IPX7纳米材料
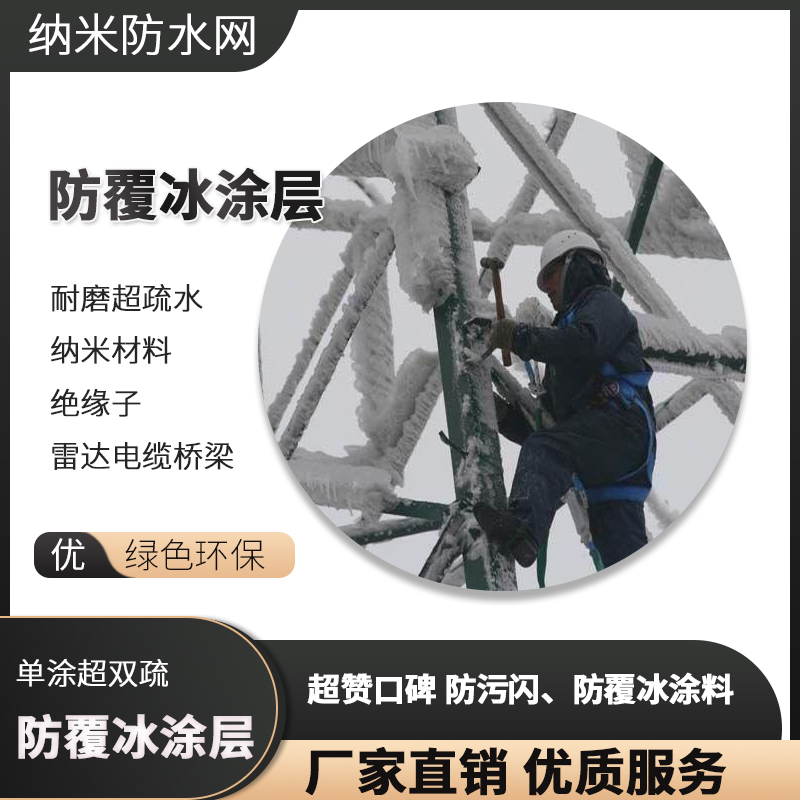
耐磨超疏水纳米材料 绝缘子架空导线电缆桥梁防覆冰涂层
耐磨超疏水纳米材料 绝缘子架空导线电缆桥梁防覆冰涂层
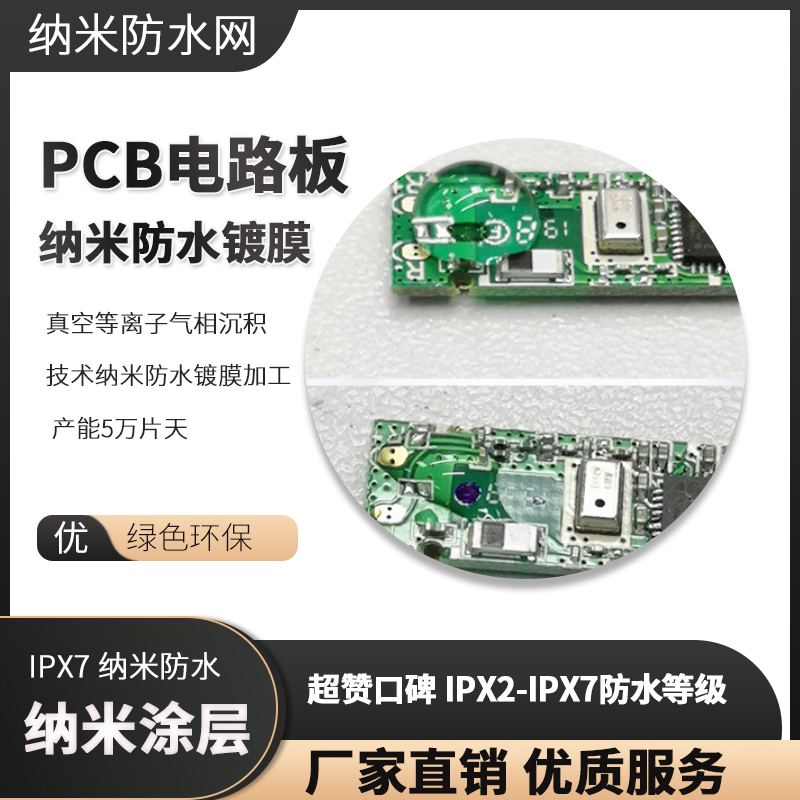
真空等离子气相沉积技术纳米防水镀膜加工 产能5万片天
真空等离子气相沉积技术纳米防水镀膜加工 产能5万片天
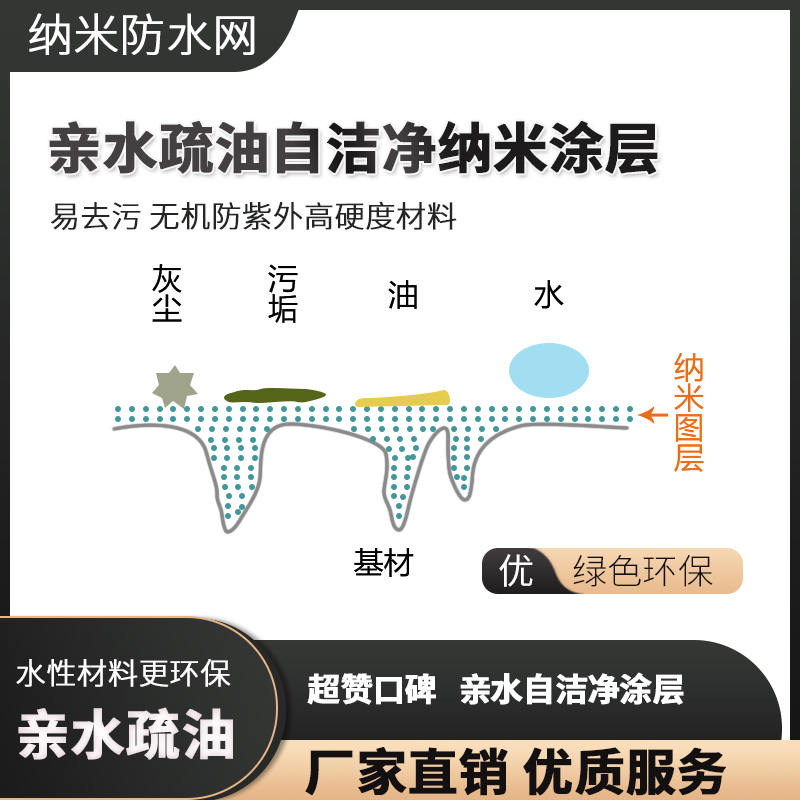
亲水疏油自洁净纳米涂层 易去污 无机防紫外高硬度材料
亲水疏油自洁净纳米涂层 易去污 无机防紫外高硬度材料

台湾超亲水防雾塑料专用 附着力好 透过率高 持久有效
台湾超亲水防雾塑料专用 附着力好 透过率高 持久有效